Coil Tubing Calculations
Every Supervisor and field hand should have an easy access to any and all field calculations they need to operate or forecast a job. Extreme Shale Performance has made all your calculations conveniently available and easy to use. Plug in your job specifications and calculate what you are looking for. Please explore our Operators handbook and see the calculations that are available on your phone or on your laptop, anywhere anytime!
Calculate ID:
OD – (2 * Wall)
1.75 – (2 * .156) = 1.438 in
Calculate Area of Tubing Wall:
( OD2 – ID2 ) * p / 4 NOTE: (p/4 =.7854)
( 1.752 – 1.4382 ) * .7854 = .781 in2
Calculate Tubing Weight Per Foot (Wall Thickness Unknown)
((((OD2 – ID2) * .7854) * 12)/ 231) * 65.5
((((2.8752 – 2.4412) * .7854) * 12) / 231) * 65.5 =
Calculate Tubing Weight per foot:
p * ( OD – Wall ) * Wall * 12 * .2833
p * ( 1.75 – .156 ) * .156 * 12 * .2833 = 2.656 lbs/ft
Calculate Buoyancy Factor:
( 65.447 – Fluid Weight, lbs/gal ) / 65.447
( 65.447 – 8.33 ) / 65.447 = .873
Calculate Weight of Tubing in Fluid:
Weight in Air * Buoyancy Factor
2.656 * .873 = 2.319 lbs/ft
Calculate Load Capacity @ Minimum Yield:
( OD2 – ID2 ) * .7854 * Yield * SF
( 1.752 – 1.4382 ) * .7854 * 80,000 * .8 = 49,997 psi
Calculate Pressure Capacity:
2 * ( Wall – .005 )* Yield / OD
2 * (.156 – .005 ) * 80,000 / 1.75 = 13,806 psi
Calculate Pipe Capacity in Barrels per Linear Foot:
ID2 * .0009714
1.4382 .0009714 = .002009 bbls/ft
Multiply by Total Length for Total Capacity in Barrels
Calculate Annular Volume in Barrels per Linear Foot:
(IDprod2 – ODcoil2 ) * .0009714
( 2.4412 – 1.752 ) * .0009714 = .00281316 bbls/ft
Multiply by Total Length for Total Capacity in Barrels
Calculate Annular Velocity, Ft/Min:
GPM * 24.51 / (IDprod2 – ODcoil2 )
84 * 24.51 / ( 4.8922 – 1.752 ) = 98.7 ft/min
Time to Displace:
Total Volume ,bbls / Pump Rate, bbl/min = Minutes
or
Total Volume ,gal / Pump Rate, gal/min = Minutes
Calculate Fluid Pressure Gradient:
Down Hole Pressure / Depth = psi/ft
or
Fluid Weight, lbs/gal * .05195 = psi/ft
Calculate Hydrostatic Pressure:
Weight, lbs/gal * .05195 * Depth
9.6 * .05195 * 11,200 = 5591 psi
Calculate Bottom Hole Pressure:
Well Head Pressure + Hydrostatic Pressure
2200 + ((9.6 * .05195 * 11,200)) = 7785.664 psi
Calculate Kill Fluid Weight:
Weight, lbs/gal + [ Well Head Pressure / ( .05195 * Depth ) ]
9.6 + ( 2200 / ( .05195 * 11,200 ) ) = 13.4 lbs/gal
Calculate Stretch due to Weight in hole, feet :
.0567 * ( Length / 1000 )2
.0567 * (12000 / 1000)2 = 8.1648 Feet
Calculate a “Free Point” for stuck tubing or the length of free pipe
L = Stretch in inches*(30000000*Area)/Force/12
Stretch = inches, from over-pull force
Area = cross-sectional area of CT pipe wall
Force =applied weight over weight of pipe in air to stretch the CT
Example:
CT OD = 1.5
CT ID = 1.282
Stretch = 120 inches
Force = 15000 lbs (Weight Indicator)
120 * 30,000,000 * .476 / 15000 /12 = 9520 feet.
Calculate Elongation Due to Temperature, feet :
Average Temperature :
( Surface Temperature + Bottom Hole Temperature ) / 2
( 70 + 210 ) / 2 = 140 Deg. F
DT :
Average Temperature – Surface Temperature
140 – 70 = 70 Deg. F
Depth * .0000828 * DT / 12
9650 * .0000828 * 70 / 12 = 4.7 ft
Calculate Specific Gravity of oil from API :
141.5 / ( 131.5 + API )
141.5 / ( 131.5 + 30 ) = .876
Calculate thermal gradient, Deg F / ft
(Bottom hole Temperature – Suface temperature) / Depth
( 195 – 60 ) / 9800 = .00138 Deg F / ft
or .138 Deg F / 100 ft
or 1.38 Deg F / 1000 ft
Calculate Pressure drop due to friction
.000077 * MW .8 * Q 1.8 * PV 2 * L / D 4.8
.000077 * 8.33 .8 * 42 1.8 * 1 2 * 10000 / 1.438 4.8 = 613.2 psi
For spooled tubing on the reel: add 10 % or x 1.1
- * 1.1 = 674.5 psi or 67.4 psi /1000 ft
MW = Fluid weight in lbs/gal
Q = Flow rate in gal / min
PV = Plastic viscosity in centipois
L = Length of pipe to flow through in feet
D = Diameter of pipe to flow through in inches
*NOTE: This is conservative compared to the Quality Charts
PHYSICAL CONSTANTS:
Viscosity of water = 1 centipoise
API gravity of water = 10 Deg. API
Fresh water n’ and k’ = 1.0 and .00002
Fresh water weighs 8.33 lbs/gal
1 cu. ft = 7.4805 gal
Water weighs 8.33 * 7.4805 = 62.312565 lbs/cu. ft
1 cu. ft = 12 in * 12 in * 12 in = 1728 cu. in
Pressure = Force / Area
62.312565 lbs / 144 sq in = .4327261458 lbf / sq in / ft or psi/ft
.4327261458 psi/ft / 8.33 lb/gal = .05194791666 (.05195) thus the constant born .052
1 bbl = 5.615 cu. ft = 42 gal
1 gal of Liquid (Cryogenic) N2 expands to 93.11 SCF
N2 expands 697 times ( more exact: 696.4 times)
Calculate KCL in pounds for % Needed:
Gallons x (Fluid weight) x % KCL wanted = lbs
80 bbl x 42 = 3360 gallons
3360 x 8.6 lbs/gal x 2% = 578 lbs KCL
Calculate rate of travel with coiled tubing
(Total bbl ÷ Pump rate in bbls/min = Total Minutes)
(Total Interval in feet ÷ minutes = ft/min)
150 bbls Acid
200 ft Interval to Place Acid
150 bbls÷ 2 bbl/min = 75 mins.
200 ft Interval ÷75 minutes = 2.6 fpm
To make 3 passes using same problem
75 minutes ÷ 3 = 25 minutes
200 ft Interval ÷ 25 minutes = 8 ft/min each pass
To Calculate Pump Rate
(Bore2 x .7854 x Stroke x # of plungers)
42 x .7854 x 8 x 3 = 301.6 in3
= 301.6 in3 x (1gal ÷ 231 in3) x (1 bbl ÷ 42 gals)
= .0312 bbl/rev
= 1 ÷ .0312 = 32.05 rev/bbl
Assume Operating range in the 80 to 90 % Efficiency Range
32.05 rev/bbl x .85% = 27.2 rev/bbl
2 bbl/min x 27.2 rev/bbl = 54.4 strokes/min
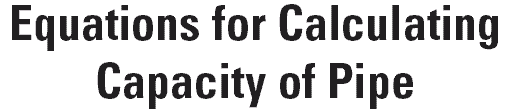
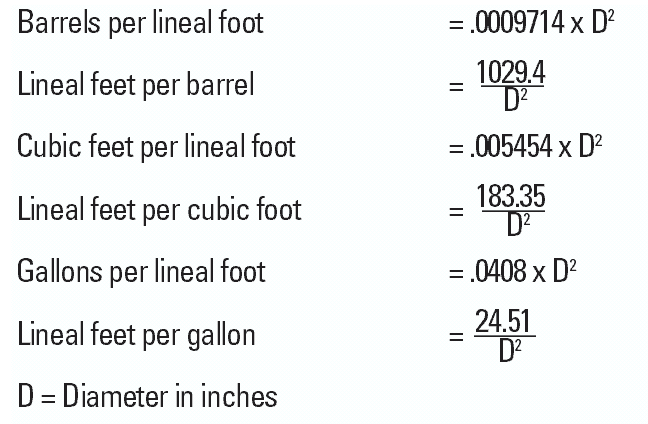
Kill Wt Fluid: PPG = PSI / .05195 X depth
(O.D. 2 – I.D. 2) X .7854 X .05195 X 65.447 =
(O.D. 2 – I.D. 2 )X 2.6703 = wt. per ft